Pengelasan laser
Dalam beberapa tahun terakhir, berkat pesatnya perkembangan industri energi baru, pengelasan laser dengan cepat merambah seluruh industri energi baru karena keunggulannya yang cepat dan stabil.Diantaranya, peralatan las laser menyumbang proporsi aplikasi tertinggi di seluruh industri energi baru.
Pengelasan laser dengan cepat menjadi pilihan pertama di semua lapisan masyarakat karena kecepatannya yang cepat, kedalaman yang besar, dan deformasi yang kecil.Dari pengelasan titik hingga pengelasan butt, pengelasan build-up dan seal, pengelasan laser memberikan presisi dan kontrol yang tak tertandingi.Ini memainkan peran penting dalam produksi dan manufaktur industri, termasuk industri militer, perawatan medis, ruang angkasa, suku cadang mobil 3C, lembaran logam mekanis, energi baru dan industri lainnya.
Dibandingkan dengan teknologi pengelasan lainnya, pengelasan laser memiliki kelebihan dan kekurangan yang unik.
Keuntungan:
1. Kecepatan cepat, kedalaman besar dan deformasi kecil.
2. Pengelasan dapat dilakukan pada suhu normal atau dalam kondisi khusus, dan peralatan pengelasannya sederhana.Misalnya, sinar laser tidak melayang dalam medan elektromagnetik.Laser dapat mengelas di lingkungan vakum, udara, atau gas tertentu, dan dapat mengelas material yang menembus kaca atau transparan terhadap sinar laser.
3. Dapat mengelas bahan tahan api seperti titanium dan kuarsa, dan juga dapat mengelas bahan yang berbeda dengan hasil yang baik.
4. Setelah laser terfokus, kepadatan dayanya tinggi.Rasio aspeknya bisa mencapai 5:1, dan bisa mencapai hingga 10:1 saat mengelas perangkat berdaya tinggi.
5. Pengelasan mikro dapat dilakukan.Setelah sinar laser terfokus, dapat diperoleh titik kecil dan dapat diposisikan secara akurat.Hal ini dapat diterapkan pada perakitan dan pengelasan benda kerja mikro dan kecil untuk mencapai produksi massal otomatis.
6. Dapat mengelas area yang sulit dijangkau dan melakukan pengelasan jarak jauh non-kontak, dengan fleksibilitas tinggi.Terutama dalam beberapa tahun terakhir, teknologi pemrosesan laser YAG telah mengadopsi teknologi transmisi serat optik, yang memungkinkan teknologi pengelasan laser dipromosikan dan diterapkan secara lebih luas.
7. Sinar laser mudah dipisahkan dalam ruang dan waktu, dan beberapa sinar dapat diproses di beberapa lokasi secara bersamaan, memberikan kondisi untuk pengelasan yang lebih presisi.
Cacat:
1. Akurasi perakitan benda kerja harus tinggi, dan posisi balok pada benda kerja tidak boleh menyimpang secara signifikan.Hal ini dikarenakan ukuran titik laser setelah pemfokusan kecil dan lapisan lasnya sempit sehingga sulit untuk menambahkan bahan logam pengisi.Jika keakuratan perakitan benda kerja atau keakuratan posisi balok tidak memenuhi persyaratan, maka rentan terjadi cacat pengelasan.
2. Biaya laser dan sistem terkait tinggi, dan investasi satu kali yang besar.
Cacat pengelasan laser yang umum dalam pembuatan baterai litium
1. Porositas pengelasan
Cacat umum pada pengelasan laser adalah pori-pori.Kolam lelehan las dalam dan sempit.Selama proses pengelasan laser, nitrogen menyerang kolam cair dari luar.Selama proses pendinginan dan pemadatan logam, kelarutan nitrogen menurun seiring dengan penurunan suhu.Ketika logam cair mendingin dan mulai mengkristal, kelarutannya akan turun tajam dan tiba-tiba.Pada saat ini, sejumlah besar gas akan mengendap membentuk gelembung.Jika kecepatan mengambang gelembung lebih kecil dari kecepatan kristalisasi logam, pori-pori akan terbentuk.
Dalam aplikasi di industri baterai litium, kita sering menemukan bahwa pori-pori sangat mungkin timbul selama pengelasan elektroda positif, namun jarang terjadi selama pengelasan elektroda negatif.Hal ini karena elektroda positif terbuat dari aluminium dan elektroda negatif terbuat dari tembaga.Selama pengelasan, aluminium cair di permukaan telah mengembun sebelum gas internal meluap sepenuhnya, mencegah gas meluap dan membentuk lubang besar dan kecil.Stomata kecil.
Selain penyebab pori-pori yang disebutkan di atas, pori-pori juga mencakup udara luar, kelembapan, minyak permukaan, dll. Selain itu, arah dan sudut hembusan nitrogen juga akan mempengaruhi pembentukan pori-pori.
Lalu bagaimana cara mengurangi terjadinya pori-pori las?
Pertama, sebelum pengelasan, noda minyak dan kotoran pada permukaan material yang masuk perlu dibersihkan tepat waktu;dalam produksi baterai litium, pemeriksaan material yang masuk merupakan proses yang penting.
Kedua, aliran gas pelindung harus disesuaikan dengan faktor-faktor seperti kecepatan pengelasan, daya, posisi, dll., dan tidak boleh terlalu besar atau terlalu kecil.Tekanan jubah pelindung harus disesuaikan berdasarkan faktor-faktor seperti kekuatan laser dan posisi fokus, dan tidak boleh terlalu tinggi atau terlalu rendah.Bentuk nosel jubah pelindung harus disesuaikan dengan bentuk, arah dan faktor lasan lainnya sehingga jubah pelindung dapat menutupi area pengelasan secara merata.
Ketiga, mengontrol suhu, kelembaban dan debu di udara di bengkel.Suhu dan kelembapan lingkungan akan mempengaruhi kadar air pada permukaan substrat dan gas pelindung, yang pada gilirannya akan mempengaruhi pembentukan dan keluarnya uap air di kolam cair.Jika suhu dan kelembapan lingkungan terlalu tinggi, maka akan terdapat terlalu banyak kelembapan pada permukaan substrat dan gas pelindung, sehingga menghasilkan uap air dalam jumlah besar, sehingga mengakibatkan pori-pori.Jika suhu dan kelembapan lingkungan terlalu rendah, kelembapan pada permukaan substrat dan gas pelindung akan terlalu sedikit, sehingga mengurangi pembentukan uap air, sehingga mengurangi pori-pori;biarkan personel kualitas mendeteksi nilai target suhu, kelembaban dan debu di stasiun pengelasan.
Keempat, metode beam swing digunakan untuk mengurangi atau menghilangkan pori-pori pada pengelasan penetrasi dalam laser.Karena penambahan ayunan selama pengelasan, ayunan bolak-balik balok ke lapisan las menyebabkan peleburan kembali bagian lapisan las secara berulang-ulang, yang memperpanjang waktu tinggal logam cair di kolam las.Pada saat yang sama, defleksi balok juga meningkatkan masukan panas per satuan luas.Rasio kedalaman dan lebar las berkurang, sehingga menyebabkan munculnya gelembung, sehingga menghilangkan pori-pori.Di sisi lain, ayunan balok menyebabkan lubang kecil berayun sesuai, yang juga dapat memberikan gaya pengadukan pada kolam las, meningkatkan konveksi dan pengadukan pada kolam las, dan mempunyai efek menguntungkan dalam menghilangkan pori-pori.
Kelima, frekuensi pulsa, frekuensi pulsa mengacu pada jumlah pulsa yang dipancarkan oleh sinar laser per satuan waktu, yang akan mempengaruhi masukan panas dan akumulasi panas di kolam cair, dan kemudian mempengaruhi bidang suhu dan bidang aliran di kolam cair. kolam.Jika frekuensi pulsa terlalu tinggi akan menyebabkan masukan panas yang berlebihan pada kolam cair, menyebabkan suhu kolam cair menjadi terlalu tinggi, menghasilkan uap logam atau unsur lain yang mudah menguap pada suhu tinggi, sehingga mengakibatkan pori-pori.Jika frekuensi pulsa terlalu rendah, maka akan menyebabkan akumulasi panas yang tidak mencukupi di kolam cair, menyebabkan suhu kolam cair menjadi terlalu rendah, mengurangi pelarutan dan keluarnya gas, sehingga mengakibatkan pori-pori.Secara umum, frekuensi pulsa harus dipilih dalam kisaran yang wajar berdasarkan ketebalan substrat dan kekuatan laser, dan hindari terlalu tinggi atau terlalu rendah.
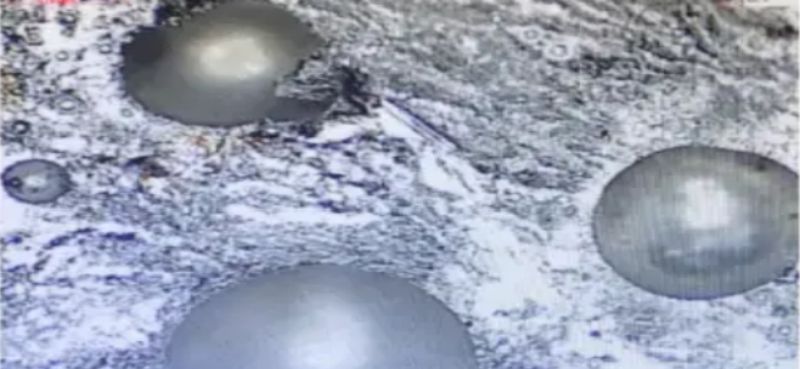
Lubang las (las laser)
2. Percikan las
Percikan yang dihasilkan selama proses pengelasan, pengelasan laser akan sangat mempengaruhi kualitas permukaan lasan, dan akan mencemari serta merusak lensa.Kinerja umumnya adalah sebagai berikut: setelah pengelasan laser selesai, banyak partikel logam muncul di permukaan material atau benda kerja dan menempel pada permukaan material atau benda kerja.Performa yang paling intuitif adalah saat mengelas dalam mode galvanometer, setelah beberapa saat menggunakan lensa pelindung galvanometer, akan terdapat lubang padat di permukaan, dan lubang tersebut disebabkan oleh percikan pengelasan.Lampu las akan mudah terhalang dalam jangka waktu yang lama, dan akan terjadi masalah pada lampu las, yang mengakibatkan serangkaian masalah seperti pengelasan rusak dan pengelasan virtual.
Apa penyebab percikan?
Pertama, rapat daya, semakin besar rapat daya, semakin mudah menimbulkan hujan rintik-rintik, dan hujan rintik-rintik berhubungan langsung dengan rapat daya.Ini adalah masalah yang sudah berusia satu abad.Setidaknya hingga saat ini, industri belum mampu mengatasi masalah cipratan air, dan hanya bisa dikatakan sudah sedikit berkurang.Dalam industri baterai litium, percikan adalah penyebab terbesar korsleting baterai, namun hal ini belum mampu mengatasi akar permasalahannya.Dampak percikan pada baterai hanya dapat dikurangi dari sudut pandang perlindungan.Misalnya, lingkaran lubang pembuangan debu dan penutup pelindung ditambahkan di sekitar bagian pengelasan, dan deretan pisau udara ditambahkan secara melingkar untuk mencegah dampak percikan atau bahkan kerusakan pada baterai.Pengrusakan lingkungan, produk dan komponen di sekitar stasiun pengelasan dapat dikatakan telah menghabiskan banyak cara.
Sedangkan untuk mengatasi masalah hujan rintik-rintik, hanya dapat dikatakan bahwa mengurangi energi pengelasan membantu mengurangi hujan rintik-rintik.Mengurangi kecepatan pengelasan juga dapat membantu jika penetrasi tidak mencukupi.Namun dalam beberapa persyaratan proses khusus, pengaruhnya kecil.Ini adalah proses yang sama, mesin yang berbeda dan kumpulan material yang berbeda memiliki efek pengelasan yang sangat berbeda.Oleh karena itu, terdapat aturan tidak tertulis dalam industri energi baru, satu set parameter pengelasan untuk satu peralatan.
Kedua, jika permukaan bahan atau benda kerja yang diproses tidak dibersihkan, noda minyak atau polutan juga akan menimbulkan percikan yang serius.Saat ini yang paling mudah adalah membersihkan permukaan bahan yang diproses.
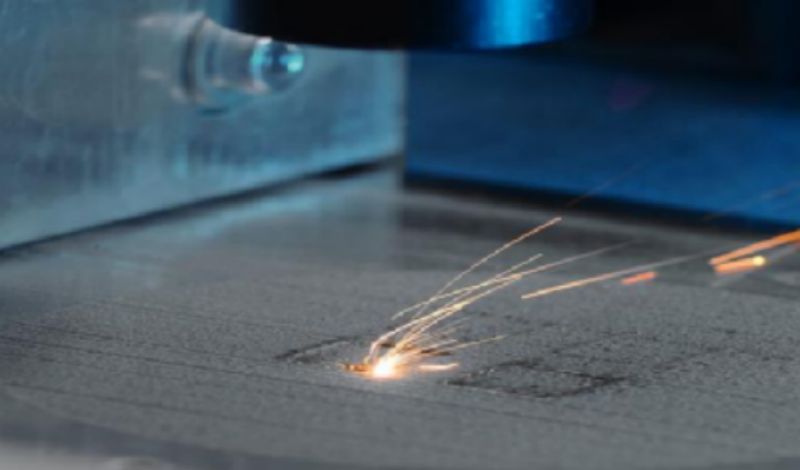
3. Reflektivitas pengelasan laser yang tinggi
Secara umum, refleksi yang tinggi mengacu pada fakta bahwa bahan pemrosesan memiliki resistivitas yang kecil, permukaan yang relatif halus, dan tingkat penyerapan yang rendah untuk laser inframerah-dekat, yang menyebabkan emisi laser dalam jumlah besar, dan karena sebagian besar laser digunakan. secara vertikal Karena bahan atau sedikit kemiringan, sinar laser yang kembali memasuki kepala keluaran, dan bahkan sebagian dari cahaya yang kembali digabungkan ke dalam serat pemancar energi, dan ditransmisikan kembali sepanjang serat ke dalam laser, membuat komponen inti di dalam laser terus berada pada suhu tinggi.
Jika reflektifitas terlalu tinggi selama pengelasan laser, solusi berikut dapat diambil:
3.1 Gunakan lapisan anti pantulan atau rawat permukaan material: melapisi permukaan bahan las dengan lapisan anti pantulan dapat secara efektif mengurangi reflektifitas laser.Lapisan ini biasanya merupakan bahan optik khusus dengan reflektifitas rendah yang menyerap energi laser dan bukan memantulkannya kembali.Dalam beberapa proses, seperti pengelasan kolektor arus, sambungan lunak, dll., permukaannya juga dapat diembos.
3.2 Sesuaikan sudut pengelasan: Dengan mengatur sudut pengelasan, sinar laser dapat mengenai bahan las pada sudut yang lebih tepat dan mengurangi terjadinya pantulan.Biasanya, sinar laser yang mengenai permukaan material yang akan dilas tegak lurus adalah cara yang baik untuk mengurangi pantulan.
3.3 Menambahkan penyerap tambahan: Selama proses pengelasan, sejumlah penyerap tambahan, seperti bubuk atau cairan, ditambahkan ke dalam lasan.Peredam ini menyerap energi laser dan mengurangi reflektifitas.Penyerap yang tepat perlu dipilih berdasarkan bahan las spesifik dan skenario aplikasi.Dalam industri baterai litium, hal ini tidak mungkin terjadi.
3.4 Gunakan serat optik untuk mengirimkan laser: Jika memungkinkan, serat optik dapat digunakan untuk mengirimkan laser ke posisi pengelasan untuk mengurangi reflektifitas.Serat optik dapat mengarahkan sinar laser ke area pengelasan untuk menghindari paparan langsung ke permukaan bahan las dan mengurangi terjadinya pantulan.
3.5 Menyesuaikan parameter laser: Dengan menyesuaikan parameter seperti daya laser, panjang fokus, dan diameter fokus, distribusi energi laser dapat dikontrol dan pantulan dapat dikurangi.Untuk beberapa bahan reflektif, mengurangi daya laser mungkin merupakan cara efektif untuk mengurangi pantulan.
3.6 Gunakan pemecah sinar: Pemisah sinar dapat mengarahkan sebagian energi laser ke perangkat penyerapan, sehingga mengurangi terjadinya pantulan.Perangkat pemisah berkas biasanya terdiri dari komponen optik dan peredam, dan dengan memilih komponen yang sesuai dan menyesuaikan tata letak perangkat, reflektifitas yang lebih rendah dapat dicapai.
4. Pengelasan melemahkan
Dalam proses pembuatan baterai lithium, proses manakah yang lebih mungkin menyebabkan undercutting?Mengapa terjadi undercutting?Mari kita analisa.
Undercut, umumnya bahan baku pengelasan tidak tercampur dengan baik satu sama lain, celah terlalu besar atau muncul alur, kedalaman dan lebar pada dasarnya lebih besar dari 0,5 mm, panjang total lebih besar dari 10% panjang las, atau lebih besar dari standar proses produk panjang yang diminta.
Dalam keseluruhan proses pembuatan baterai lithium, undercutting lebih mungkin terjadi, dan umumnya terjadi pada pra-pengelasan penyegelan dan pengelasan pelat penutup silinder dan pra-pengelasan penyegelan dan pengelasan pelat penutup cangkang aluminium persegi.Alasan utamanya adalah pelat penutup penyegel perlu bekerja sama dengan cangkang untuk Pengelasan, proses pencocokan antara pelat penutup penyegel dan cangkang rentan terhadap celah las yang berlebihan, alur, keruntuhan, dll., sehingga sangat rentan terhadap undercut. .
Lalu apa yang menyebabkan terjadinya undercut?
Jika kecepatan pengelasan terlalu cepat, logam cair di belakang lubang kecil yang mengarah ke tengah lasan tidak akan punya waktu untuk mendistribusikan kembali, sehingga terjadi pemadatan dan pemotongan pada kedua sisi lasan.Mengingat situasi di atas, kita perlu mengoptimalkan parameter pengelasan.Sederhananya, ini adalah percobaan berulang untuk memverifikasi berbagai parameter, dan terus melakukan DOE hingga parameter yang sesuai ditemukan.
2. Kesenjangan las yang berlebihan, alur, keruntuhan, dll. pada bahan las akan mengurangi jumlah logam cair yang mengisi celah tersebut, sehingga lebih mungkin terjadi undercut.Ini adalah pertanyaan tentang peralatan dan bahan baku.Apakah bahan baku pengelasan memenuhi persyaratan material yang masuk dalam proses kami, apakah keakuratan peralatan memenuhi persyaratan, dll. Praktik yang normal adalah terus-menerus menyiksa dan memukuli pemasok dan orang yang bertanggung jawab atas peralatan tersebut.
3. Jika energi turun terlalu cepat pada akhir pengelasan laser, lubang kecil bisa runtuh, mengakibatkan pemotongan lokal.Pencocokan kekuatan dan kecepatan yang tepat dapat secara efektif mencegah pembentukan undercut.Seperti kata pepatah lama, ulangi eksperimen, verifikasi berbagai parameter, dan lanjutkan DOE hingga Anda menemukan parameter yang tepat.
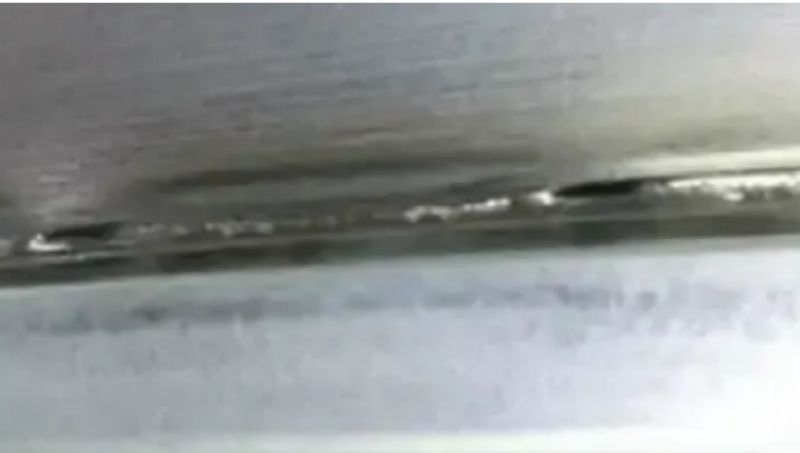
5. Runtuhnya pusat las
Jika kecepatan pengelasan lambat, kolam lelehan akan semakin besar dan lebar, sehingga meningkatkan jumlah logam cair.Hal ini dapat mempersulit pemeliharaan tegangan permukaan.Jika logam cair menjadi terlalu berat, bagian tengah las bisa tenggelam dan membentuk cekungan dan lubang.Dalam hal ini, kepadatan energi perlu dikurangi secara tepat untuk mencegah keruntuhan kumpulan lelehan.
Dalam situasi lain, celah pengelasan hanya runtuh tanpa menyebabkan perforasi.Tidak diragukan lagi, ini adalah masalah kesesuaian peralatan.
Pemahaman yang tepat tentang cacat yang dapat terjadi selama pengelasan laser dan penyebab berbagai cacat memungkinkan pendekatan yang lebih tepat sasaran untuk menyelesaikan masalah pengelasan yang tidak normal.
6. Retakan las
Retakan yang muncul selama pengelasan laser kontinu sebagian besar merupakan retakan termal, seperti retakan kristal dan retakan pencairan.Penyebab utama terjadinya retakan ini adalah besarnya gaya penyusutan yang ditimbulkan oleh lasan sebelum benar-benar mengeras.
Ada juga penyebab retakan pada pengelasan laser berikut ini:
1. Desain las yang tidak masuk akal: Desain geometri dan ukuran las yang tidak tepat dapat menyebabkan konsentrasi tegangan pengelasan, sehingga menyebabkan retakan.Solusinya adalah mengoptimalkan desain las untuk menghindari konsentrasi tegangan pengelasan.Anda dapat menggunakan las offset yang sesuai, mengubah bentuk las, dll.
2. Ketidaksesuaian parameter pengelasan: Pemilihan parameter pengelasan yang tidak tepat, seperti kecepatan pengelasan yang terlalu cepat, daya yang terlalu tinggi, dll., dapat menyebabkan perubahan suhu yang tidak merata di area pengelasan, yang mengakibatkan tegangan dan retakan pengelasan yang besar.Solusinya adalah menyesuaikan parameter pengelasan agar sesuai dengan material tertentu dan kondisi pengelasan.
3. Persiapan permukaan pengelasan yang buruk: Kegagalan membersihkan dan merawat permukaan pengelasan dengan benar sebelum pengelasan, seperti menghilangkan oksida, minyak, dll., akan mempengaruhi kualitas dan kekuatan lasan dan mudah menyebabkan retakan.Solusinya adalah dengan membersihkan dan melakukan perawatan awal pada permukaan pengelasan secara memadai untuk memastikan bahwa kotoran dan kontaminan di area pengelasan dapat diatasi secara efektif.
4. Kontrol masukan panas pengelasan yang tidak tepat: Kontrol masukan panas yang buruk selama pengelasan, seperti suhu yang berlebihan selama pengelasan, laju pendinginan lapisan pengelasan yang tidak tepat, dll., akan menyebabkan perubahan struktur area pengelasan, yang mengakibatkan retakan. .Solusinya adalah dengan mengontrol suhu dan laju pendinginan selama pengelasan untuk menghindari panas berlebih dan pendinginan yang cepat.
5. Pelepasan tegangan yang tidak mencukupi: Perlakuan pelepas tegangan yang tidak memadai setelah pengelasan akan mengakibatkan pelepasan tegangan yang tidak mencukupi pada area yang dilas, yang akan dengan mudah menyebabkan keretakan.Solusinya adalah dengan melakukan penanganan pereda tegangan yang tepat setelah pengelasan, seperti perlakuan panas atau perlakuan getaran (alasan utama).
Sedangkan untuk proses pembuatan baterai litium, proses mana yang lebih mungkin menyebabkan keretakan?
Umumnya retakan rawan terjadi pada saat pengelasan penyegelan, seperti pengelasan penyegelan cangkang baja silinder atau cangkang aluminium, pengelasan penyegelan cangkang aluminium persegi, dll. Selain itu, pada proses pengemasan modul, pengelasan pengumpul arus juga rawan terjadi. retak.
Tentu saja, kita juga dapat menggunakan kawat pengisi, pemanasan awal, atau metode lain untuk mengurangi atau menghilangkan retakan tersebut.
Waktu posting: 01-Sep-2023